Some clients have asked us “what is a certificate of conformity” over the years, and…
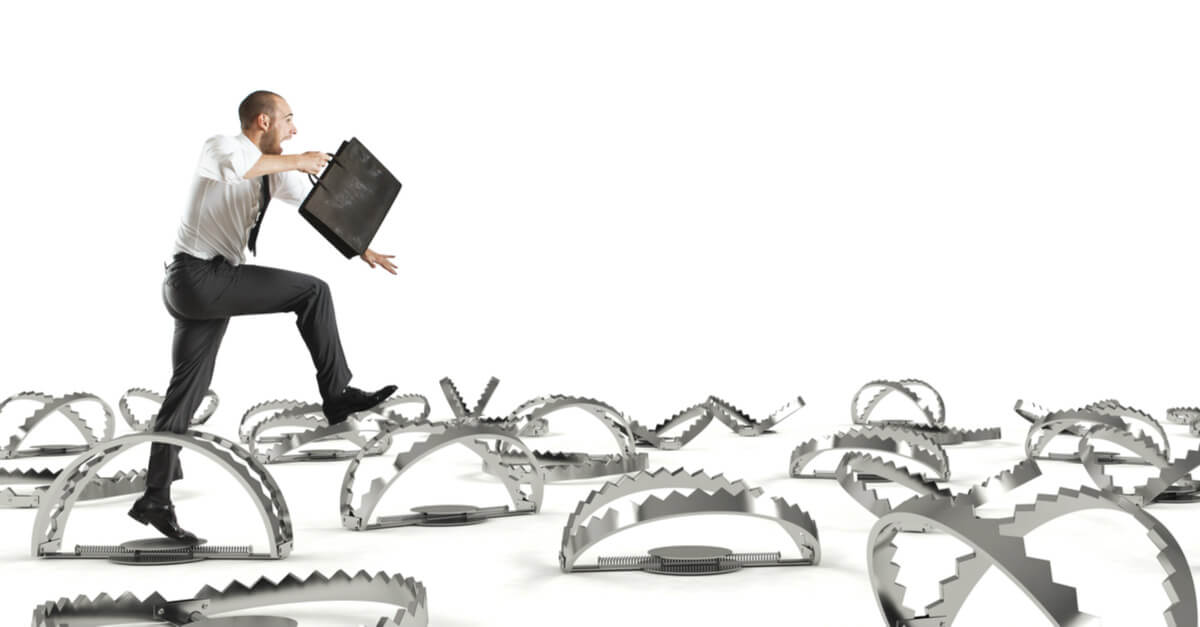
The 7 Most Common Product Launch Pitfalls in China
BY RENAUD ANJORAN
More and more companies work with Chinese manufacturers on new product developments. And, in most cases, things don’t turn out the way customers want.
I thought I’d highlight the most common product launch pitfalls I have observed for electrical and/or mechanical products.
1. Thinking that “the factory is an expert in manufacturing and all will be good”
We have run into many people who think this way. This is typical among companies that essentially do trading (buy and then resell without major transformation). They don’t want to get involved and they don’t have the resources for that.
Well, at least you need to know what competencies and equipment the manufacturer needs to have, otherwise you can’t select the right manufacturer…
And you need to be able to set up a plan and monitor its implementation — or you need to work with an engineering firm on this. Otherwise, you won’t be able to evaluate whether what the manufacturer tells you makes sense or not.
2. Keeping product design and process development separated
Some companies work with a design house, then they throw a design ‘over a wall’ to some engineering staff, who then again ‘throw drawings over a wall’ to a factory’s purchasing and manufacturing departments. The result is not pretty.
All these people need to communicate. Feedback loops are very helpful. Otherwise, decisions made upstream will cause very serious issues (extra costs, higher complexity and longer time to market, etc.) down the road.
3. Starting to work on process engineering too late
This is related to point 2. If you wait until product design is finalized before manufacturing engineers start to wonder “how to build this?”, the launch might happen weeks later than it should.
Have manufacturing people start to work as the product design is getting developed, not after.
4. Failing to confirm the quality of key components
This is a classic in China.
Especially if those components are also, themselves, custom-made. If they were manufactured for the first time, or if the manufacturer is unproven, the probability of quality issues is very high.
Don’t wait until assembly has started to find out that 50% of a certain part (already delivered and paid in full) can’t be used for production…
5. Failing to develop the testing stations in time
It’s not just about building products, it’s also about making sure they are good! We have seen examples where the testing equipment takes 2 months to develop. It definitely needs to be in the plan from the start…
6. Not training the operators before aiming at mass production
Was a new (dedicated) layout set up for this production? Was special tooling developed? Are some operations a bit out of the ordinary? The operators need training!
Are quality/safety requirements different from other customers’? Are testing stations custom-made? Inspectors also need training!
7. Making projections on production volume without running some tests
Chinese suppliers are consistently over-optimistic. And it means they tend to under-deliver. When a complex mesh of inputs need to come together neatly at the same time and the planning doesn’t allow for any issue, the norm is ending up 2-3 months behind schedule.
In contrast, let’s look at best practices.
In the automotive industry, tier-1 suppliers (as well as the car plants themselves) are forced to demonstrate they can run production from A to Z at a certain rate. Here is the usual approach:
- Ensure all the inputs are ready
- Set a goal of X pieces per hour, set things in motion
- Record problems, stop, work on them
- Again, set a goal of 1.3X pieces per hour, set things in motion
- Again, work on fixing problems so things can go faster next time
- And so on until a certain goal — which corresponds to the desired run rate at launch — has been achieved
- Launch mass production and work on the remaining kinks that come up… the key here becomes consistency
This is how a lot of the training gets done, when mistakes can be made and management is looking for issues to address.
From: qualityinspection
This Post Has 0 Comments