Some clients have asked us “what is a certificate of conformity” over the years, and…
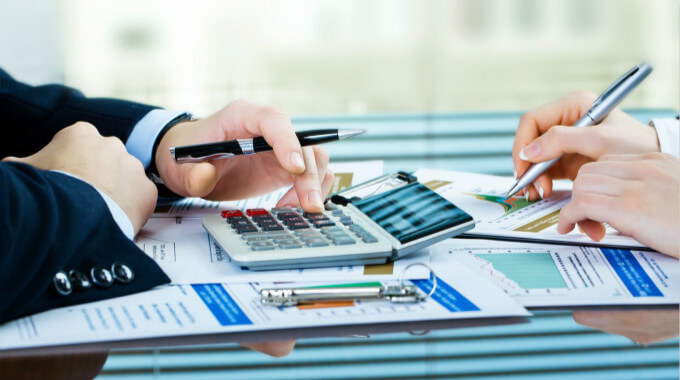
Carbon vs. Alloy vs. Stainless: Steel Grades You Might Buy in China
BY RENAUD ANJORAN
There are basically 3 types of steel that are used when it comes to product manufacturing:
- Carbon Steel
- Alloy Steel
- Stainless Steel
Each of these types of steel has a variety of grades that comprise of different amounts of iron and carbon (the basic elements of steel) and additional alloys.
When selecting the right metal for your job, there are several factors that you need to consider:
- Hardness– capacity to resist abrasion, but also difficulty in being cut or drilled
- Strength– amount of force necessary to deform the metal
- Toughness– ability to resist to stress (and not break)
- Malleability – ability of the metal to deform
- Weldability– ability to be welded (it’s a function of melting point, heat conductivity, etc.)
Let’s go through the 3 types: carbon, alloy, and carbon.
1. Carbon Steel
Carbon Steel (an alloy of steel and carbon) gets corroded but it is hard — the more carbon content, the harder the steel. Low-carbon steel is strong and tough and can be case-hardened if needed. High-carbon steel can be heat treated to make it a lot harder, however, in this condition it tends to be more brittle and more difficult to work with.
Common applications for carbon steel:
- Tubes, plates, bolts, signs, furniture, fencing and many other common metal parts are made in low carbon steel.
- Professional kitchen knives, cutting tools in CNC machines, drill bits, saws, masonry nails are all made with high carbon steel. The high hardness gives blades and cutting tools a sharp edge that lasts, however, with this hardness come brittleness which means products tend to break easier.
The disadvantage of high-carbon steel is that it is more expensive and harder to machine than alloys with less carbon. It is appropriate when rust is not a concern and when the product doesn’t need to withstand tensile stress (it doesn’t really bend, and it breaks more easily).
2. Alloy Steel
Alloy Steel (which has additional chemical elements added to improve certain properties) – some of the most common alloying elements are manganese, nickel, chromium, molybdenum, vanadium, silicon, and boron.
The improved properties that alloy steels have over carbon steel are; strength, hardness, toughness, wear resistance, corrosion resistance, and hardenability.
Common applications for alloy steels:
- Construction and architecture where strength, toughness and corrosion resistance are a pre-requisite for the material.
- Jewelry, household items, cutlery, cook wear are all manufactured from alloy steel.
Alloy steels can be split into two categories, low alloy steels and high alloy steels. Low alloy steels have less than 8% total alloying elements in the composition, these steels have better hardness and resistance to wear over carbon steel but tend to have less tensile strength.
The high alloy steels have more than 8% alloying elements and have better properties than those of the low alloying steels.
3. Stainless Steel
Stainless Steel (an alloy of steel and chromium) doesn’t corrode easily, but it is not as hard.
Any product that will be in constant contact with liquids is a good candidate for a steel alloy with high chromium content. Stainless steel is an alloy of steel with a minimum of 10.5% and up to 30% chromium that gives this steel its unique properties.
Stainless steel is broken into five categories:
a) Austenitic – Austenitic Stainless Steels are classed as the 200 and 300 series and the alloying elements are basically steel with 18% chromium and 8% nickel and a low carbon content. The most common steel produced is the 304 Stainless Steel, commonly used for pipework, mining equipment, food and beverage, kitchenware and architecture.
b) Ferritic – Ferritic Stainless Steels are plain chromium stainless steels where the chromium content can vary between 12% and 18%, these also have a low carbon content, similar to the austenitic range. There are classified as the 400 series. This range of stainless steels are magnetic and have good ductility and corrosion resistance. Typical applications are heat exchangers, automotive fasteners, furnace parts, heater parts.
c) Duplex – Duplex Stainless Steels contain a high level of chromium between 18% and 28% as well nickel between 4% and 8%. These two-high element level gives a mix of austenitic and ferritic structure, hence the name of duplex stainless steel.
Duplex stainless steel is generally twice as hard as plain austenitic or ferritic stainless steels. They have slightly better toughness and ductility properties than ferritic grades but not as good values when compared to the austenitic grades. Duplex grades have higher strength, good weldability, good toughness, and have high resistance to stress corrosion cracking. Typical applications are hot water tanks, brewing tanks, process plant equipment, swimming pool structures.
d) Martensitic – Martensitic Stainless Steels are plain chromium steels containing between 12% and 18% as well as having a relatively high content of carbon of up to 1.2%. Martensitic grades have a better corrosion (not as much as austenitic grades) and wear resistance than other Stainless Steel grades and can be heat treated to achieve high hardness values. These grades are magnetic in the annealed and hardened state. Typical applications include cutlery, cook-wear, surgical and dental instruments, springs, scissors, industrial blades, vehicle stampings, screwdrivers, pliers, and staple guns.
e) Precipitation Hardening – Precipitation Hardening Stainless Steels (PHSS) are a chromium and nickel with at least one other alloying element (copper, aluminum, titanium, niobium or molybdenum). PHSS grades provide an optimum combination of both martensitic and austenitic grade properties. Like martensitic grades, they are known for their ability to gain high strength through heat treatment and they also have the corrosion resistance of austenitic stainless steel.
The most well-known precipitation hardening stainless steel is 17-4 PH. The name comes from the additions 17% Chromium and 4% Nickel. It also contains 4% Copper and 0.3% Niobium. 17-4 PH is also known as stainless steels grade 630. Typical applications include dental drills and reamers, aircraft components, shaver heads, surgical needles, and aerospace applications.
Common stainless steel grades
You can get a chart about these grades, their main attributes, and examples of common applications
The three most common steel grades we encounter in China are:
- 201 – inexpensive and very common
- 304 – the most common grade of stainless steel
- 316 – a more expensive grade, with better resistance to corrosion
4. A word about stainless iron
Stainless iron is sometimes used, too. The main difference with this material is that it has less than 0.6%Ni or no Ni element in it, such as 403 (12Cr12). It’s widely used in chemical industry and construction industry. Any magnetic iron alloy containing more than 12% chromium having a body-centered cubic structure is also known as stainless iron.
Most Common Heat Treatment Processes
Heat treatment is the process of heating and cooling the metal without changing its physical shape. There are different heat treatment processes which when applied to different steels can change the properties of that steel, such as its hardness, toughness and even softening, which are all determined by the change in the steel microstructure.
Hardening – A steel with sufficient amount of carbon content can be hardened by heating it up and then rapidly quenching it. This process creates an austenite microstructure which can be ferrite, martensite or cementite.
Tempering – This process is carried out on carbon steels that have been hardened in order to reduce the brittleness of the steel. The temperature of tempering will depend upon the desired result for the function of the steel product, the lower the tempering temperature the better the strength and hardness.
Annealing – Annealing steel involves heating up the steel past its critical temperature and then letting it cool down very slowly. This results in the steel becoming more machinable and workable from a forming aspect.
Normalizing – This is a similar process to annealing where the steel is heated and cooled slowly, normally just left to cool in room temperature air. This gives steel a microstructure of ferrite and cementite which has higher strength and hardness but lower ductility properties.
Carburizing – Carburizing is also known as case-hardening which is a process of infusing additional carbon to the surface of low carbon steel and then subjecting it to the hardening process. The outer carbon steel will have higher hardness where the inner core will remain tough.
How to test a metal to ensure it is the right grade?
The best is to conduct both physical testing and chemical analysis.
The most common physical tests are:
- Tensile test (applying tension until failure)
- Hardness (or durometry) test, which can be done in different ways
Chemical analysis is usually done with an X-ray fluorescence tester.
From: qualityinspection
This Post Has 0 Comments